Indice
- Introduzione
- Analisi delle materie prime ceramiche
- I processi di trasformazione industriale
- La cottura: trasformazione definitiva delle proprietà
- Smalti e materiali vetrificanti: il contributo artificiale
- Classificazione tecnica: naturale, artificiale o ibrido?
- Aspetti ambientali e sostenibilità
- Innovazioni contemporanee nel settore
- Graniglie tecniche Sicer: il contributo ingegnerizzato alla superficie ceramica
- Conclusioni scientifiche sulla natura della ceramica
- FAQ
Introduzione
La classificazione dei materiali in “naturali” e “artificiali” rappresenta un tema chiave nella scienza dei materiali, ma anche un terreno ambiguo quando si tratta di materiali trasformati come la ceramica. In ambito tecnico, un materiale naturale è una sostanza presente in natura senza modifiche sostanziali (come legno, pietra, argilla cruda), mentre un materiale artificiale è ottenuto attraverso processi di sintesi chimica e non esiste in natura (come le resine polimeriche o la plastica). Tra questi due estremi si colloca una categoria intermedia: i materiali trasformati, ovvero materiali naturali modificati da processi industriali, pur senza una ricombinazione molecolare ex novo.
La ceramica – in tutte le sue declinazioni, dalle piastrelle tradizionali alle ceramiche tecniche – sfugge a una classificazione univoca. Sebbene le sue materie prime siano naturali, i processi cui è sottoposta (macinazione, miscelazione, pressatura, cottura a temperature estreme) la trasformano in modo così radicale da renderla un materiale nuovo, con proprietà strutturali, chimiche e ottiche profondamente diverse da quelle di partenza.
Per i professionisti del settore ceramico – in particolare per i responsabili R&D e i tecnici di laboratorio – comprendere la natura ibrida della ceramica non è solo una questione accademica. È un punto di partenza per:
- scegliere le giuste formulazioni in base al tipo di utilizzo richiesto (indoor/outdoor, tecnico/estetico);
- sviluppare nuove soluzioni decorative o funzionali;
- valutare l’impatto ambientale dei processi produttivi e dei materiali impiegati;
- posizionare correttamente il prodotto sul mercato, anche dal punto di vista normativo e di sostenibilità.
In questo articolo analizzeremo, con approccio scientifico e tecnico, tutte le fasi che portano un materiale naturale a diventare un prodotto ceramico avanzato, valutandone le implicazioni classificative e applicative. Una riflessione utile per comprendere dove si colloca oggi la ceramica nel panorama dei materiali contemporanei.
Analisi delle materie prime ceramiche
Origine naturale
Le principali materie prime ceramiche (argille, feldspati, caolino, quarzo) derivano da rocce di origine naturale. Sono formate da processi geologici millenari e si presentano come miscele eterogenee di silicati di alluminio, spesso accompagnati da impurezze minerali che ne influenzano il comportamento tecnico.
Composizione chimica
Queste materie mostrano composizioni variabili:
- Argille: alluminosilicati idrati, plastiche e refrattarie
- Feldspati: fondenti alcalini, facilitano la vetrificazione
- Quarzo: inerte, regola il ritiro e la dilatazione termica
La natura chimica è chiave per capire la reattività durante la cottura.
Variabilità naturale
Le stesse argille possono cambiare colore, plasticità o contenuto di ossidi in funzione della cava, del deposito geologico, della granulometria.
I processi di trasformazione industriale
Preparazione delle materie prime
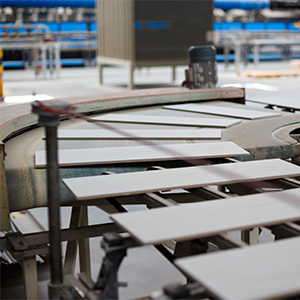
Il primo passo nella produzione ceramica è la preparazione delle materie prime, una fase che richiede precisione e controllo. I materiali grezzi – principalmente argille, feldspati, quarzo e caolino – vengono sottoposti a un ciclo di frantumazione meccanica e successiva micronizzazione per ottenere una granulometria controllata e reattiva. Questo passaggio è cruciale per garantire una distribuzione uniforme delle particelle, ridurre la presenza di impurità e ottimizzare la reattività chimico-fisica nei passaggi successivi.
La polvere ottenuta viene poi miscelata in impianti a umido o a secco, spesso con l’aggiunta di additivi o leganti organici, al fine di migliorare le proprietà reologiche e l’attitudine alla pressatura. L’obiettivo è ottenere un impasto omogeneo, stabile e facilmente lavorabile, in grado di garantire costanza prestazionale lungo tutta la linea produttiva.
Formatura
Una volta preparato, l’impasto viene trasformato in semilavorato attraverso diverse tecniche di formatura, scelte in base alla tipologia di prodotto desiderato:
- Pressatura: la più comune nella produzione di piastrelle, prevede l’utilizzo di presse idrauliche che compattano la polvere in stampi, ottenendo lastre con densità omogenea e geometrie precise.
- Estrusione: utilizzata per prodotti a sezione continua come klinker e listelli, consente di modellare impasti plastici spinti attraverso una filiera, utile per forme articolate o strutture cave.
- Colaggio: impiegato per manufatti complessi come sanitari, sfrutta la colabilità di impasti fluidi in stampi porosi che assorbono l’acqua e lasciano un residuo solido aderente alla forma desiderata.
Ciascun metodo influisce sul comportamento meccanico e termico del materiale, rendendo la scelta della tecnologia di formatura un aspetto strategico in funzione della destinazione d’uso del prodotto ceramico.
Essiccazione
Terminata la formatura, il prodotto crudo (detto anche “verde”) viene sottoposto a essiccazione controllata, con l’obiettivo di eliminare l’umidità libera presente nell’impasto. Questo passaggio è fondamentale per prevenire tensioni interne e fessurazioni che potrebbero comprometterne l’integrità in fase di cottura.
L’essiccazione avviene in appositi forni o tunnel ad aria calda, e la sua efficacia influisce direttamente su:
- porosità residua
- ritiro dimensionale
- resistenza meccanica iniziale
Parametri come temperatura, velocità dell’aria e durata vengono calibrati in base alla composizione dell’impasto e al formato del pezzo.
Trasformazioni fisiche pre-cottura
Durante queste fasi, le materie prime perdono progressivamente le loro caratteristiche originarie. L’argilla, ad esempio, da materiale plastico e malleabile si trasforma in corpo rigido e fragile, pronto per affrontare la cottura.
Le trasformazioni fisiche e meccaniche includono:
- variazioni strutturali della matrice argillosa
- orientamento delle particelle durante la pressatura
- inizio di fenomeni di sinterizzazione superficiale in presenza di additivi
A questo punto, il materiale non è più una semplice somma delle sue materie prime, ma un sistema tecnico pre-ingegnerizzato, pronto per subire l’ultima, cruciale metamorfosi: la cottura.
La cottura: trasformazione definitiva delle proprietà
La cottura rappresenta il punto di non ritorno nel ciclo produttivo ceramico: è il momento in cui il materiale passa da uno stato crudo e instabile a uno stato solido, coerente e definitivo. Questo avviene attraverso un insieme di trasformazioni chimiche, fisiche e strutturali indotte dal calore, che rendono il materiale ceramico un’entità completamente nuova rispetto alla somma delle sue materie prime originarie.
Reazioni chimiche durante la cottura
Durante la cottura – che avviene tipicamente tra i 1000 °C e i 1250 °C, a seconda della composizione dell’impasto – si sviluppano numerose reazioni termoindotte:
- Deidrossilazione dell’argilla: le argille perdono acqua strutturale, trasformandosi da fillosilicati in fasi amorfe più stabili.
- Fusione parziale dei fondenti (es. feldspati): questi componenti iniziano a liquefarsi formando una fase vetrosa.
- Sinterizzazione: le particelle solide si saldano fra loro, riducendo la porosità e aumentando la resistenza meccanica.
- Cristallizzazione di nuove fasi: come la mullite (3Al₂O₃·2SiO₂), che si forma da reazioni tra caolino e silice, conferendo elevate proprietà meccaniche e resistenza termica.
Queste reazioni trasformano il corpo ceramico in una struttura eterogenea, composta da fasi vetrose e cristalline, che ne definiscono le proprietà finali.
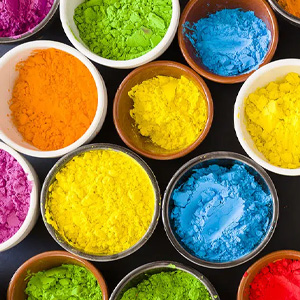
Variazioni strutturali e ottiche
A livello microstrutturale, la cottura determina:
- riduzione della porosità (da >10% a <1% per alcuni gres tecnici)
- stabilizzazione dimensionale
- sviluppo del colore attraverso l’interazione tra ossidi coloranti e fase vetrosa
- variazioni della riflettanza e della trasparenza
Il materiale ceramico, una volta cotto, diventa inerte, igienico, meccanicamente stabile e resistente agli agenti chimici e atmosferici. È questa stabilità a renderlo idoneo per applicazioni in ambienti industriali, pubblici o outdoor.
Impatto sul comportamento tecnico
Le caratteristiche tecniche che derivano dalla cottura sono decisive per le performance del prodotto finale:
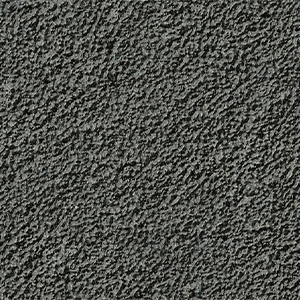
- resistenza alla flessione (fino a 40–50 MPa per gres porcellanato)
- coefficiente di dilatazione termica controllato (essenziale per pavimentazioni riscaldanti)
- durabilità nel tempo anche sotto sollecitazioni meccaniche o termiche
Anche le proprietà antiscivolo, quando richieste, sono influenzate dalla microstruttura finale ottenuta dopo la cottura, che può essere progettata con l’aggiunta di graniglie, rilievi o trattamenti superficiali come nella linea NEXT EXPERIENCE SURFACES di Sicer.
Irreversibilità del processo
Una volta completata, la cottura non è reversibile. Non esiste alcun trattamento fisico o chimico che consenta di riportare il materiale alle sue condizioni originarie. Questo aspetto segna la completa transizione da materiale naturale a materiale ingegnerizzato, con proprietà che dipendono tanto dalla composizione iniziale quanto dalla curva termica applicata.
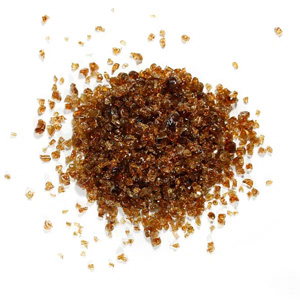
Smalti e materiali vetrificanti: il contributo artificiale
Sebbene la ceramica nasca da materie prime naturali, una parte consistente delle sue proprietà estetiche e funzionali dipende da elementi interamente sviluppati in ambito industriale, come gli smalti, le fritte vetrificanti e i materiali decorativi. Questi componenti non solo completano il ciclo produttivo, ma ne modificano radicalmente le performance.
Composizione e funzione degli smalti ceramici
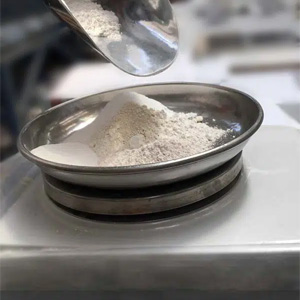
Lo smalto ceramico è una miscela vetrosa che, applicata sulla superficie del supporto ceramico e successivamente cotta, forma un sottile rivestimento protettivo e decorativo.
Dal punto di vista chimico, lo smalto è composto da:
- ossidi vetrofondenti (Na₂O, K₂O, CaO)
- ossidi formatori di vetro (SiO₂, B₂O₃)
- stabilizzanti e modificatori (Al₂O₃, ZnO, TiO₂)
- eventuali pigmenti e opacizzanti
Questi componenti vengono premiscelati e sottoposti a fusione ad alta temperatura (1300–1500 °C), poi raffreddati bruscamente e macinati: nasce così la fritta ceramica, base di quasi tutti gli smalti industriali. Questo processo è completamente artificiale: nessuna delle fasi avviene in natura.
Smalti funzionali e speciali
Negli ultimi decenni si è passati da smalti “neutri” a formulazioni avanzate, capaci di conferire proprietà tecniche e prestazioni estetiche elevate alle superfici ceramiche. Gli smalti non hanno più un ruolo passivo di protezione, ma diventano parte integrante della progettazione funzionale del prodotto.
Tra le principali funzionalità:
- resistenza chimica e meccanica migliorata, utile in ambienti industriali, contract o outdoor;
- interazione ottimizzata con gli inchiostri digitali, per garantire la stabilità cromatica in cottura;
- versatilità estetica, grazie a diverse finiture superficiali (lucide, opache, satinate) e differenti curve di fusione.
Sicer propone una gamma completa di smalti ceramici per applicazioni tradizionali o digitali, formulati per garantire:
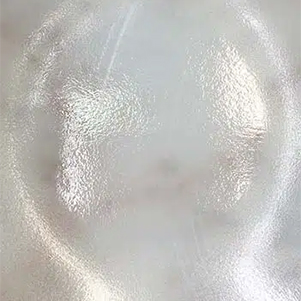
- fusibilità controllata e compatibilità con i supporti,
- profondità visiva e trasparenza quando richiesto,
- interazione mirata con le graniglie nelle applicazioni in rilievo tramite colla digitale.
Gli smalti Sicer sono studiati per adattarsi alle esigenze specifiche di ogni ciclo produttivo e si integrano perfettamente con le tecnologie di decorazione contemporanee, comprese le applicazioni digitali multilivello e l’uso sinergico con graniglie e colle.
Inchiostri digitali e decorazioni avanzate
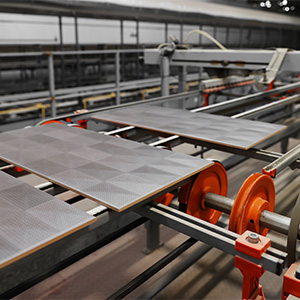
La decorazione ceramica ha subito una trasformazione radicale con l’introduzione della stampa digitale inkjet, che ha sostituito i metodi tradizionali serigrafici e rotocalcografici. Gli inchiostri ceramici digitali sono composti da sospensioni di ossidi e pigmenti micronizzati in veicoli organici o solventi specifici, progettati per garantire stabilità di stampa, fusibilità e interazione con gli smalti.
Oggi il settore si sta evolvendo verso una nuova generazione di inchiostri ad alto valore aggiunto, capaci non solo di decorare ma anche di ridurre l’impatto ambientale del ciclo produttivo.
Sicer è attiva in prima linea con due linee di ricerca avanzata:
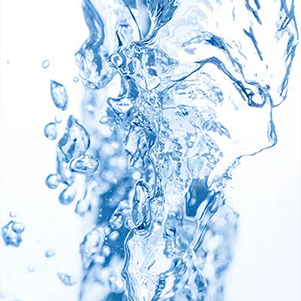
- Inchiostri LOW EMISSION (LE) a base eco-solvente, brevettati, con:
- riduzione certificata di VOC, aldeidi e COT fino al 70% rispetto ai migliori eco-ink presenti sul mercato,
- assenza di odore e alta compatibilità con tutte le testine di stampa,
- ottima resa estetica e cromatica,
- base completamente customizzabile in termini di colore e effetto.
- Inchiostri WATER BASED (WB) attualmente in fase avanzata di sviluppo, pensati per coniugare le performance grafiche con il massimo della compatibilità ambientale e per preparare il settore all’evoluzione normativa futura in ottica ESG.
A questi si affianca la colla digitale a base acqua, progettata per applicazioni in rilievo tramite graniglie: disponibile in versioni per alte e basse temperature, garantisce precisione grafica, ottima adesione e emissioni minime.
Grazie a questi investimenti, Sicer conferma il proprio ruolo di partner tecnologico per una decorazione ceramica sostenibile, certificata e ad alte prestazioni, contribuendo in modo concreto agli obiettivi ESG dei produttori ceramici.
Il ruolo dei materiali decorativi nella prestazione finale
Oltre alla valenza estetica, i materiali decorativi influenzano:
- resistenza all’abrasione (es. graniglie dure vs smalti teneri)
- coefficiente di attrito (tramite texture e applicazioni strutturate)
- resistenza ai raggi UV (inchiostri inorganici stabili alla luce)
- risultati cromatici post-cottura, che dipendono dall’interazione con la curva termica
In sintesi, smalti, fritte e inchiostri costituiscono il cuore tecnologico del rivestimento ceramico. Sono il frutto della ricerca industriale e ne rappresentano il contributo artificiale più evidente: una componente insostituibile, senza la quale il materiale ceramico moderno perderebbe le sue caratteristiche più distintive. E Sicer lo sa bene.
Classificazione tecnica: naturale, artificiale o ibrido?
Il dibattito sulla classificazione della ceramica tra i materiali naturali o artificiali non è soltanto semantico, ma ha implicazioni rilevanti per i tecnici di laboratorio, i responsabili R&D e i buyer del settore ceramico. Una corretta definizione aiuta a posizionare il prodotto all’interno delle filiere industriali, a confrontarlo con materiali alternativi e a orientare le scelte progettuali in termini di sostenibilità, prestazioni e normative.
Dove si colloca la ceramica?
Analizzando composizione, processi produttivi e comportamento finale, la ceramica non può essere considerata né pienamente naturale né completamente artificiale, ma appartiene con chiarezza alla categoria dei materiali trasformati.
Criterio tecnico | Ceramica |
Origine delle materie prime | Naturale (argilla, feldspati, quarzo) |
Interventi industriali | Estesi e irreversibili |
Composizione finale | Diversa da quella originale |
Struttura microcristallina | In gran parte ingegnerizzata |
Funzionalizzazione | Estetica, tecnica, meccanica |
Durante il ciclo produttivo, le materie prime ceramiche subiscono modificazioni tali da non poter essere più separate, né ricondotte alle forme originarie. Il prodotto finale è un materiale composito, vetroso e cristallino, inerte, indeformabile e ad alte prestazioni.
Confronto con altri materiali da costruzione
Per inquadrare meglio il posizionamento della ceramica, può essere utile confrontarla con altri materiali ampiamente utilizzati nel settore edilizio e architettonico:
Materiale | Origine | Processo | Classificazione tecnica |
Legno | Naturale | Minimo | Naturale |
Cemento | Naturale + Artificiale | Alta | Artificiale (reattivo) |
Vetro | Naturale | Alta | Trasformato (amorfo) |
Plastica | Sintetica | Altissima | Artificiale |
Ceramica | Naturale | Alta | Materiale trasformato (ibrido) |
Questo posizionamento ibrido conferisce alla ceramica versatilità applicativa, ma impone anche una maggiore consapevolezza nella gestione del ciclo produttivo, nella comunicazione tecnica e nelle scelte di design.
Implicazioni per il settore ceramico
Classificare la ceramica come materiale trasformato ad alto contenuto tecnologico ha ricadute concrete su vari fronti:
- Nella comunicazione tecnica con progettisti, architetti e buyer
- Nella valutazione ambientale e LCA
- Nella ricerca di soluzioni decorative e funzionali che sfruttino appieno le possibilità offerte dalla sua natura ingegnerizzata
Comprendere e comunicare correttamente la natura ibrida della ceramica non è solo una questione accademica, ma uno strumento per generare valore lungo tutta la filiera, dalla formulazione al marketing tecnico.
Aspetti ambientali e sostenibilità
La riflessione sulla natura della ceramica non può prescindere da una valutazione del suo impatto ambientale. In un contesto industriale sempre più attento a circolarità, decarbonizzazione e standard ESG, comprendere la sostenibilità del materiale ceramico è fondamentale per i responsabili R&D, i buyer e i decisori strategici.
Impatto ambientale delle materie prime
Le materie prime utilizzate nella produzione ceramica – argille, feldspati, quarzo – derivano da processi estrattivi non rinnovabili. Tuttavia:
- sono abbondanti in natura,
- non richiedono processi chimici complessi per essere utilizzate,
- non rilasciano sostanze pericolose durante l’impiego o a fine vita.
Il vero nodo ambientale non è l’origine naturale in sé, ma il modo in cui queste risorse vengono estratte, trasportate e gestite. L’uso di fornitori locali o a basso impatto logistico riduce significativamente l’impronta di carbonio.
Processi produttivi ad alto consumo energetico
La criticità principale del settore ceramico è l’elevato fabbisogno energetico:
- essiccazione e cottura richiedono grandi quantità di calore (spesso da fonti fossili),
- la cottura a ciclo continuo comporta emissioni dirette di CO₂, ossidi di azoto (NOₓ), zolfo (SOₓ) e particolato.
È in questa fase che le aziende possono implementare strategie di sostenibilità:
- ottimizzazione dei cicli termici,
- recupero di calore dai forni,
- utilizzo di combustibili alternativi o miscele metano/idrogeno,
digitalizzazione del controllo di processo per ridurre sprechi e scarti.
Confronto con materiali artificiali
Rispetto a materiali totalmente artificiali (come resine, PVC, linoleum), la ceramica:
- non emette VOC (composti organici volatili),
- non degrada sotto l’azione del calore o dei raggi UV,
- non rilascia microplastiche,
ha una durata media superiore ai 30 anni in applicazioni edilizie.
Questa longevità intrinseca compensa in parte l’elevato impatto della fase di produzione, rendendo la ceramica una scelta preferibile in ottica LCA (Life Cycle Assessment).
Riciclabilità e gestione del fine vita
Il materiale ceramico cotto è chimicamente inerte, non biodegradabile, ma riciclabile in numerose applicazioni secondarie. Tra i principali impieghi:
- frantumazione per sottofondi stradali, massetti drenanti e inerti da riempimento;
- inclusione in impasti ceramici secondari per prodotti rustici o tecnici a bassa plasticità;
- uso nei cementi pozzolanici, come sostituzione parziale di clinker ad alta emissione;
- applicazione in prodotti fonoassorbenti o isolanti industriali.
In parallelo, molte aziende ceramiche hanno attivato pratiche interne di economia circolare, tra cui:
- recupero degli scarti crudi (impasti, graniglie, smalti non cotti),
- reintegro dei residui di smalto o inchiostro all’interno dei cicli successivi,
- riutilizzo delle acque di processo, mediante impianti di ricircolo e trattamento.
Anche Sicer è attivamente impegnata su questo fronte: negli stabilimenti produttivi vengono implementati sistemi di riutilizzo delle acque di processo, riducendo il consumo idrico complessivo e migliorando l’efficienza ambientale dell’intero ciclo decorativo. Questo approccio, inserito in una visione più ampia di sostenibilità certificata, contribuisce agli obiettivi ESG di filiera e alla transizione verso una ceramica industriale più responsabile.
Il caso Sicer: innovazione e sostenibilità integrata
Sicer ha investito in modo strategico nella ricerca di soluzioni decorative digitali a basso impatto ambientale, con particolare attenzione alla riduzione delle emissioni VOC e all’adeguamento ai criteri ESG.
Le principali innovazioni comprendono:
- inchiostri digitali LOW EMISSION, a base solvente con formula brevettata, che riducono in modo significativo le emissioni di Composti Organici Volatili (VOC), aldeidi e COT, migliorando le condizioni ambientali in produzione;
- inchiostri digitali WATER BASED, attualmente in fase avanzata di sviluppo, ideati per combinare sostenibilità e performance grafica in ottica futura;
- colle digitali a base acqua, utilizzate per applicazioni in rilievo con graniglie, che garantiscono aderenza, precisione estetica ed emissioni ridotte.
Queste soluzioni non solo migliorano l’impatto ambientale del ciclo decorativo, ma costituiscono un elemento chiave nella strategia ESG di molti produttori ceramici. In un mercato sempre più attento alla tracciabilità, alla sicurezza chimica e alla trasparenza, Sicer si propone come partner tecnologico per la transizione sostenibile dell’industria ceramica.
Innovazioni contemporanee nel settore
L’evoluzione del settore ceramico negli ultimi vent’anni ha conosciuto un’accelerazione notevole, spinta da tre driver principali: digitalizzazione dei processi, funzionalizzazione delle superfici e sostenibilità ambientale. Per i responsabili R&D e tecnici di laboratorio, tenere traccia di queste trasformazioni significa anticipare trend di mercato e orientare lo sviluppo prodotto su logiche prestazionali e normative sempre più complesse.
Materiali decorativi avanzati
I materiali decorativi non sono più semplici strumenti estetici, ma veri e propri agenti funzionali in grado di influenzare le performance della superficie ceramica.
Oggi, grazie a formulazioni complesse e ad applicazioni multistrato, le decorazioni possono integrare:
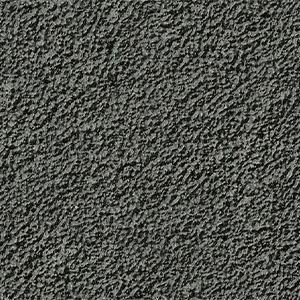
- effetti ottici avanzati (metallizzati, perlescenti, opalescenti),
- resistenze meccaniche differenziate (graniglie dure per zone di passaggio intenso),
- funzioni specifiche come l’antibatterico o la fotocatalisi (es. biossido di titanio attivato da UV).
Le micro-graniglie calibrate proposte da Sicer nella linea NEXT EXPERIENCE SURFACES sono un chiaro esempio di come la decorazione possa agire anche sul coefficiente di attrito, migliorando le proprietà antiscivolo pur mantenendo elevata la pulibilità e la qualità estetica della superficie.
Tecnologie digitali e stampa inkjet
La transizione dalla serigrafia alla decorazione digitale inkjet ha trasformato il rapporto tra progettazione e produzione ceramica:
- si lavora su database cromatici e texture digitali,
- si integra la decorazione con la modellazione 3D delle superfici (effetti strutturati, rilievi, incisioni),
- si riduce il consumo di materie prime e si ottimizza la resa per metro quadro.
In questo contesto si inseriscono innovazioni come:
- colla digitale: consente applicazioni selettive di graniglie per creare effetti tridimensionali precisi e ripetibili;
- inchiostri a base acqua: riducono l’emissione di VOC e migliorano la sicurezza ambientale;
- software predittivi per la gestione delle curve di cottura e l’ottimizzazione cromatica in forno.
Formulazioni eco-compatibili
Le nuove richieste normative e di mercato spingono verso una chimica più pulita e trasparente. Le innovazioni in questo ambito includono:
- fritte low-emission, progettate per fondere a temperature più basse e rilasciare meno gas serra;
- smalti senza piombo o cadmio, conformi alle normative REACH;
- flussi produttivi chiusi, che riciclano acqua, scarti crudi e residui di smaltatura.
Sicer, in linea con questa direzione, ha sviluppato un’intera gamma di prodotti decorativi orientati alla sostenibilità di processo, combinando ricerca chimica con efficienza produttiva e compatibilità ambientale.
Tendenze: dalla standardizzazione alla personalizzazione
Un trend emergente è il passaggio dalla logica della produzione di massa standardizzata alla personalizzazione on-demand:
- micro-lotti su richiesta,
- decorazioni on-demand per architetti e contract,
- superfici funzionalizzate per nicchie applicative (es. sanità, horeca, rivestimenti tecnici industriali).
Questa flessibilità è resa possibile proprio dalla combinazione di materiali intelligenti e tecnologie digitali, che abilitano la realizzazione di prodotti ad alto valore aggiunto anche in piccoli volumi.
Graniglie tecniche Sicer: il contributo ingegnerizzato alla superficie ceramica
Le graniglie trasparenti ad alta resistenza (linea GHR) e le graniglie lucide per applicazioni a secco (linea GRA DRY-LUX) rappresentano una delle soluzioni tecnologicamente più evolute sviluppate da Sicer per la funzionalizzazione delle superfici ceramiche. Derivano da una selezione precisa di materie prime vetrose e da un controllo avanzato di fusione e granulazione.
Tra le caratteristiche distintive:
- trasparenza ottica elevata, che valorizza la grafica digitale;
- resistenza all’abrasione e agli agenti chimici;
- coefficiente di attrito personalizzabile, utile in ambienti ad alto traffico;
- possibilità di applicazione a umido o a secco, con ampia scelta granulometrica.
Dal punto di vista tecnico, la gamma Sicer si distingue per:
- presenza di fasi cristalline funzionali (wollastonite, plagioclasio) come evidenziato da analisi XRD;
- controllo continuo della composizione e fusibilità;
- ottimizzazione delle tensioni e planarità tramite studio preventivo con flessimetro.
Le graniglie diventano così un elemento tecnico attivo nella definizione delle prestazioni superficiali del materiale ceramico, rafforzando ulteriormente la tesi dell’articolo: la ceramica contemporanea è un sistema ingegnerizzato, in cui estetica, funzione e tecnologia convivono sinergicamente.
Scopri la gamma completa di graniglie tecniche Sicer
Conclusioni scintifiche sulla natura della ceramica
L’analisi tecnica condotta dimostra come la ceramica non possa essere classificata né come materiale puramente naturale né come materiale completamente artificiale. Si tratta di un materiale trasformato, la cui natura ibrida nasce da una combinazione complessa di:
- materie prime di origine geologica,
- processi industriali ad alto contenuto tecnologico,
- interventi funzionalizzanti avanzati (smalti, inchiostri, graniglie),
- trasformazioni chimico-fisiche irreversibili durante la cottura.
Questa natura composita è ciò che rende la ceramica un materiale così versatile e apprezzato in contesti architettonici, tecnici e decorativi.
Una nuova definizione possibile: materiale ingegnerizzato a base naturale
Possiamo definire la ceramica moderna come un materiale ingegnerizzato a base naturale, dove l’origine delle materie prime resta riconoscibile, ma il comportamento del prodotto finito è del tutto nuovo, progettato per rispondere a:
- requisiti meccanici,
- esigenze estetiche,
- vincoli normativi e ambientali.
In altre parole, la ceramica è progetto e materia insieme, risultato tangibile di un processo che fonde scienza dei materiali, ingegneria del colore, sostenibilità e cultura industriale.
Implicazioni per il settore ceramico
Per il settore ceramico, questa consapevolezza rappresenta una leva strategica:
- consente di valorizzare il know-how industriale come elemento distintivo,
- orienta le scelte di R&D verso formulazioni sempre più performanti e sostenibili,
- rafforza la posizione competitiva dei produttori che investono in innovazione.
Saper comunicare correttamente la complessità scientifica e tecnica della ceramica, senza ridurla a slogan semplicistici, diventa un fattore critico anche nella relazione con architetti, general contractor, buyer e stakeholders sensibili alla sostenibilità.
Conclusione
La domanda iniziale – ceramica: materiale naturale o artificiale? – trova una risposta solo nel riconoscimento della sua natura ibrida, ingegnerizzata, evolutiva. È questa identità complessa a costituire la vera forza del materiale ceramico contemporaneo: un equilibrio sofisticato tra radici naturali e futuro industriale.
FAQ
La ceramica è un materiale trasformato: deriva da materie prime naturali, come argille e feldspati, ma viene modificata radicalmente attraverso processi industriali – frantumazione, formatura, cottura – che ne alterano struttura, composizione e comportamento. Il risultato è un materiale ingegnerizzato, stabile e funzionale
Tecnicamente, nessuno dei due. La ceramica si colloca tra i materiali naturali e quelli artificiali, in quanto viene prodotta a partire da componenti naturali, ma subisce trasformazioni fisico-chimiche che la rendono un prodotto nuovo rispetto all’origine geologica delle sue materie prime. È corretta la definizione di materiale ibrido o trasformato.
– Naturali: materiali disponibili in natura e utilizzati con modifiche minime (es. legno, pietra, argilla grezza).
– Artificiali: materiali sintetizzati interamente in laboratorio o in impianto industriale (es. polimeri plastici, vetroresina, resine epossidiche).
– Trasformati (come la ceramica): materiali naturali sottoposti a lavorazioni profonde che modificano la loro struttura originaria.
Le materie prime ceramiche provengono da depositi geologici naturali:
– le argille derivano da rocce sedimentarie ricche di silicati di alluminio,
– i feldspati sono minerali intrusivi provenienti da rocce magmatiche,
– il quarzo è un costituente comune di molte sabbie silicee.
Queste materie vengono selezionate, raffinate e trasformate industrialmente per dare vita a piastrelle, rivestimenti e ceramiche tecniche.