Indice
- Introduzione
- Principi generali della resistenza ceramica
- Resistenza meccanica: test normativi e fattori influenti
- Resistenza all’usura e all’abrasione: classificazione PEI
- Resistenza termica e shock termico: comportamento a cicli termici
- Resistenza chimica: test e condizioni d’esposizione
- Il ruolo dei materiali vetrificanti nella resistenza
- Controllo qualità e ottimizzazione dei parametri
- Innovazioni tecnologiche per migliorare la resistenza
- Applicazioni industriali e scelta dei materiali
- Conclusione
- FAQ
Introduzione
Quando si parla di resistenza ceramica, si fa riferimento alla capacità di un materiale di mantenere le proprie caratteristiche strutturali e funzionali in presenza di sollecitazioni di vario tipo. Comprendere come funziona la resistenza ceramica è essenziale per chi lavora nella progettazione e produzione di superfici ad alte prestazioni, come piastrelle, rivestimenti e superfici tecniche.
Le tipologie principali di resistenza rilevanti in ambito industriale includono:
- Resistenza meccanica, ovvero la capacità di sopportare flessione, compressione e urto senza fratturarsi. Fondamentale per pavimenti e superfici sottoposte a carichi.
- Resistenza all’abrasione e all’usura, particolarmente importante in contesti commerciali e industriali ad alto traffico, dove si richiede durabilità nel tempo.
- Resistenza termica e agli shock termici, essenziale per superfici esposte a cicli caldo-freddo o a elevate temperature, come in esterno o in ambienti produttivi.
- Resistenza chimica, necessaria in ambienti soggetti a contatto con acidi, basi, detergenti e solventi, come nel settore alimentare, sanitario o chimico.
Questi aspetti determinano la funzionalità e la durabilità del materiale ceramico e guidano la scelta dei prodotti più idonei a seconda delle condizioni d’impiego.
Principi generali della resistenza ceramica
La resistenza di un materiale ceramico è determinata in larga parte dalla sua struttura interna e dalle interazioni chimico-fisiche tra i componenti che lo costituiscono. Le seguenti caratteristiche risultano centrali per comprenderne il comportamento in applicazioni industriali:
Struttura cristallina e legami atomici
I materiali ceramici sono costituiti da una combinazione di fasi cristalline e vetrose. Le fasi cristalline presentano strutture reticolari regolari, dove gli atomi sono legati tramite legami ionici o covalenti, entrambi caratterizzati da elevata energia di legame. Questa configurazione conferisce rigidità e stabilità, ma limita la deformabilità plastica, rendendo la ceramica più suscettibile alla frattura se sottoposta a sollecitazioni elevate e concentrate.
Meccanismi fondamentali di resistenza
A livello molecolare, la resistenza dipende dalla continuità del reticolo cristallino e dall’assenza di difetti strutturali che possano fungere da punti di innesco per le fratture. I meccanismi di coesione tra i grani, l’aderenza tra fasi e la distribuzione omogenea delle particelle contribuiscono in modo determinante alle prestazioni meccaniche e termiche.
Influenza della porosità e della microstruttura
La porosità residua, se eccessiva o mal distribuita, riduce la resistenza del materiale. Nei processi ceramici industriali, si tende a minimizzare la presenza di pori aperti o chiusi attraverso la regolazione dei parametri di cottura, della granulometria e della pressatura. La microstruttura risultante da un processo ottimizzato presenta grani uniformi e fasi ben integrate, favorendo la tenuta meccanica e la resistenza all’abrasione.
Teoria della propagazione delle microfratture
Le ceramiche, essendo materiali fragili, sono soggette a rotture di tipo brittle, cioè senza deformazione plastica preventiva. Le microfratture si innescano in presenza di difetti strutturali e si propagano rapidamente sotto carichi critici. I test normativi (es. ISO 10545-4) valutano la resistenza alla flessione proprio in funzione di questa vulnerabilità. La qualità della sinterizzazione e l’omogeneità della massa ceramica sono elementi fondamentali per contenere la propagazione delle fratture.
Resistenza meccanica: flessione, compressione, urto
La resistenza meccanica rappresenta un parametro fondamentale per valutare l’idoneità dei materiali ceramici in applicazioni soggette a carichi statici e dinamici. Le normative internazionali, come la ISO 10545-4, definiscono le metodologie per la misurazione della resistenza a flessione e compressione in laboratorio.
Analisi della resistenza a flessione
La resistenza a flessione (detta anche modulo di rottura) misura la capacità del materiale di resistere a una forza distribuita su una superficie. Viene valutata applicando un carico su una piastrella supportata in due punti, fino al punto di rottura. I valori risultanti variano in funzione di:
- dimensione e spessore del campione
- regolarità e densificazione della microstruttura
- presenza di microfessurazioni interne
Una maggiore uniformità del corpo ceramico e una cottura ben controllata contribuiscono ad aumentare la resistenza a flessione.
Resistenza a compressione: meccanismi e valori
I materiali ceramici tollerano molto bene carichi compressivi grazie alla natura rigida del reticolo cristallino. La resistenza a compressione si misura mediante carichi verticali crescenti su provini di dimensione controllata. Anche in questo caso, il valore dipende dalla densità del materiale e dall’assenza di porosità o inclusioni. La prova è meno diffusa rispetto a quella a flessione, ma rilevante in ambiti strutturali o per applicazioni verticali (es. rivestimenti portanti).
Resistenza all’urto e tenacità dei materiali ceramici
La resistenza all’urto è meno elevata nei materiali ceramici rispetto ad altri materiali strutturali, a causa della loro bassa tenacità. La tenacità descrive la capacità di assorbire energia senza fratturarsi. Per verificarla, si utilizzano test come la caduta di massa su provini ceramici o strumenti dedicati alla misurazione della propagazione di fratture. In genere, una ceramica con struttura omogenea e spessori coerenti presenta una maggiore resistenza ai piccoli urti localizzati.
Test normativi di riferimento
I principali test normativi per la valutazione delle proprietà meccaniche includono:
- ISO 10545-4: Determinazione della resistenza alla flessione e alla rottura
- ASTM C1161: Metodo per la flessione su provini rettangolari di ceramica (applicato prevalentemente alla ceramica tecnica)
Questi test sono standardizzati per garantire la comparabilità dei risultati tra diversi materiali, produttori e condizioni di prova. La documentazione dei test è spesso richiesta nelle schede tecniche dei prodotti destinati ad ambienti ad alta sollecitazione.
Resistenza all’usura e all’abrasione
La resistenza all’usura è una delle proprietà più importanti dei materiali ceramici destinati all’impiego in pavimentazioni e superfici ad alto traffico. L’usura può essere causata da attriti meccanici, sfregamento, presenza di detriti abrasivi o movimentazione di carichi. Il comportamento del materiale in questi contesti è determinante per la sua durabilità nel tempo.
Meccanismi di usura superficiale nei materiali ceramici
Nei materiali ceramici, l’usura avviene per asportazione progressiva dello smalto o della superficie esterna del supporto. L’azione meccanica costante di scarpe, ruote, sabbia e altri agenti abrasivi può generare micro-solchi, perdita di lucentezza o, nei casi più gravi, rimozione di materiale e alterazione cromatica.
L’usura si distingue in:
- abrasione superficiale (lucentezza, finitura)
- abrasione profonda (struttura, colore, smalto)
Fattori che influenzano la resistenza all’abrasione
Diversi fattori concorrono a determinare il grado di resistenza di un materiale ceramico all’usura:
- Tipo di smalto o finitura: Smalti vetrificati ad alta durezza garantiscono maggiore tenuta.
- Densità e porosità del supporto: Un supporto poroso tende a cedere più rapidamente sotto stress abrasivo.
- Spessore dello strato superficiale: Maggiore è lo spessore utile, più il materiale resiste all’erosione.
- Granulometria degli agenti abrasivi: sabbie fini possono essere più insidiose di quelle più grosse.
Classificazione PEI e metodi di test per l’usura
Il metodo normativo di riferimento per la determinazione della resistenza all’usura è la norma ISO 10545-7, che definisce la classificazione PEI (Porcelain Enamel Institute). Questa metodologia prevede l’esposizione del campione ceramico a cicli di abrasione standardizzati con agenti abrasivi specifici.
La scala PEI si articola come segue:
Classe PEI | Destinazione d’uso consigliata |
PEI 1 | Bagni e camere da letto (traffico leggero) |
PEI 2 | Zone residenziali escluse cucine e ingressi |
PEI 3 | Aree residenziali ad uso moderato |
PEI 4 | Ambienti residenziali e commerciali a medio traffico |
PEI 5 | Ambienti pubblici, industriali, commerciali intensi |
La prova misura la variazione di aspetto superficiale e perdita di materiale in funzione dei cicli.
Ruolo degli smalti e trattamenti superficiali nella resistenza all’usura
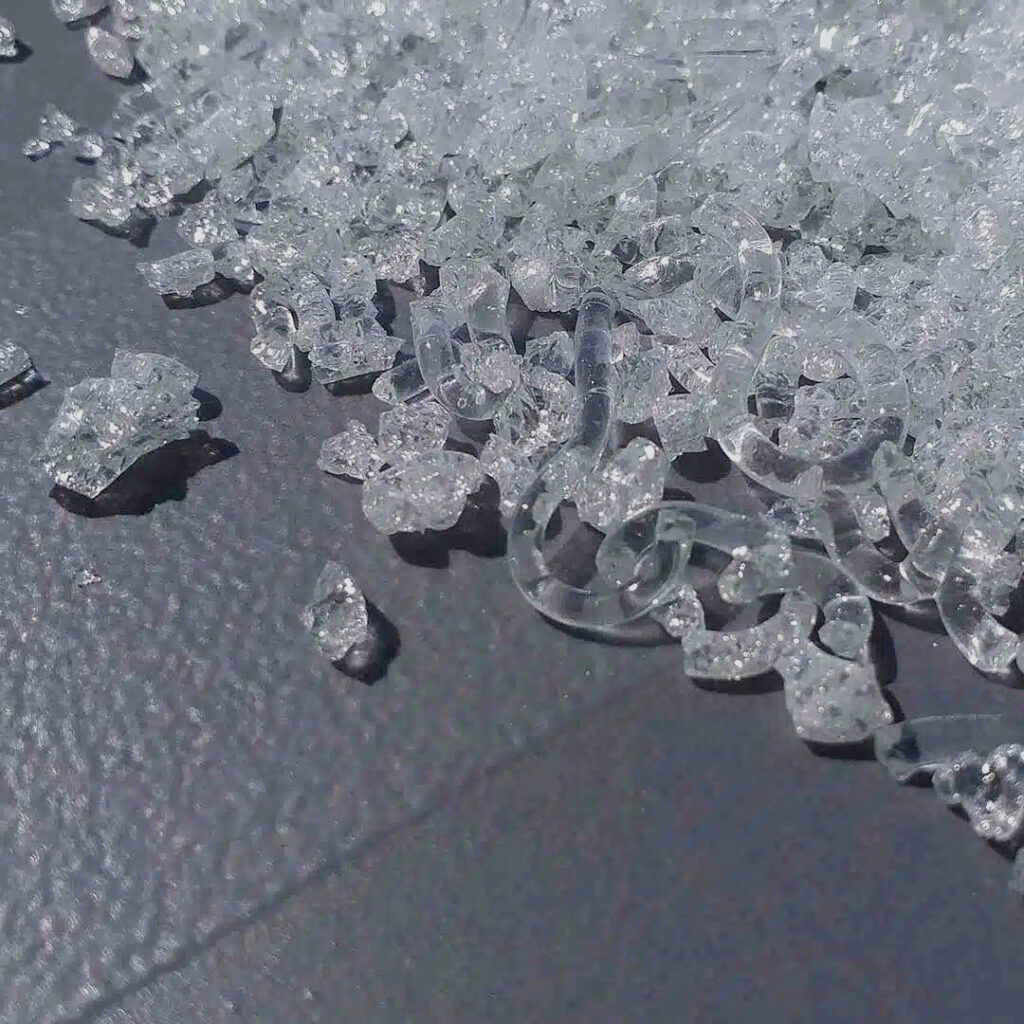
La scelta dello smalto e dei materiali vetrificanti influisce in modo diretto sulla resistenza all’abrasione delle superfici ceramiche. Smalti con composizione vetrificata e alta durezza contribuiscono a migliorare la tenuta superficiale. In funzione delle esigenze applicative, si possono adottare diverse tecnologie superficiali basate su graniglie tecniche.
Sicer mette a disposizione un’ampia gamma di graniglie ad alta resistenza studiate per incrementare le prestazioni superficiali. Tra queste:
- la linea NEXT EXPERIENCE SURFACES, realizzata con micro graniglie a granulometria calibrata, consente di ottenere superfici opache, antiriflesso, resistenti agli agenti chimici e facilmente pulibili;
- la serie GHR – High Resistance Grits, pensata per pavimenti soggetti a stress intensi, permette di ottenere superfici naturalmente materiche, antiscivolo, resistenti all’abrasione e con eccellente resa grafica anche nei toni scuri;
- la linea GRA – Dry Lux, specifica per applicazione a secco e lappatura a specchio, consente invece di realizzare superfici estremamente brillanti e compatte, con elevata resistenza chimica, pulibilità e planarità, grazie a una selezione ottimizzata di fritta e granulometria calibrata.
Tutte queste soluzioni integrano l’expertise di Sicer nella progettazione di materiali superficiali che conciliano estetica e prestazione tecnica, adattandosi a differenti cicli di produzione e destinazioni d’uso.
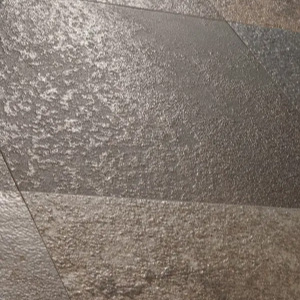
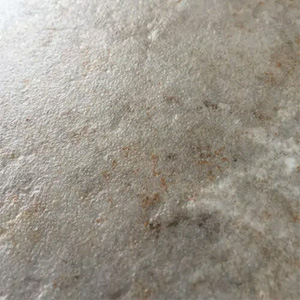
Resistenza termica e shock termico
I materiali ceramici, per la loro natura inorganica e non metallica, possiedono una buona stabilità termica, che li rende idonei per applicazioni in ambienti soggetti a variazioni di temperatura anche rilevanti. Tuttavia, il comportamento alle sollecitazioni termiche dipende da vari fattori microstrutturali e deve essere valutato attraverso prove specifiche.
Comportamento dei materiali ceramici alle variazioni di temperatura
Le ceramiche rispondono alle variazioni termiche con espansioni e contrazioni volumetriche, che possono generare tensioni interne, soprattutto in presenza di fasi eterogenee o discontinuità strutturali. Se le sollecitazioni superano la soglia di elasticità del materiale, possono verificarsi microfratture o delaminazioni tra smalto e supporto.
Coefficiente di dilatazione termica e sue implicazioni
Il coefficiente di dilatazione termica lineare (α) misura la variazione dimensionale del materiale in funzione della temperatura. Una scarsa compatibilità tra il coefficiente del supporto e quello dello smalto può generare tensioni differenziali durante la cottura o nelle fasi d’impiego, compromettendo la resistenza meccanica e l’integrità estetica del prodotto.
L’ottimizzazione delle composizioni ceramiche prevede quindi una scelta bilanciata di materie prime e vetrificanti per ridurre le differenze tra le fasi coinvolte.
Resistenza al gelo e ai cicli termici
La resistenza al gelo è un requisito fondamentale per i materiali ceramici destinati all’esterno. I test previsti dalle norme UNI e ISO (come ISO 10545-12) prevedono cicli di congelamento e scongelamento in presenza d’acqua per simulare le condizioni reali di esposizione. L’eventuale porosità residua, se aperta e capillare, può assorbire acqua e causare rotture interne in seguito all’espansione per congelamento.
La qualità della pressatura e l’assenza di microcavità sono essenziali per garantire una buona resistenza al gelo.
Shock termico: cause, meccanismi e prevenzione
Lo shock termico è causato da variazioni rapide e significative di temperatura (es. passaggi da +150°C a temperatura ambiente), che possono generare fratture improvvise in materiali con bassa conducibilità termica o elevata rigidità.
La norma ISO 10545-9 definisce i criteri di test per lo shock termico nelle piastrelle smaltate, sottoponendo i campioni a immersioni alternate in acqua fredda e calda. Un prodotto è considerato conforme se, al termine del ciclo, non presenta evidenti segni di deterioramento (crepe, distacchi, variazione di lucentezza o colore).
La progettazione ottimale del ciclo di cottura, l’uso di materie prime con stabilità termica elevata e l’assenza di porosità residua sono fattori chiave nella prevenzione di danni da shock termico.
Resistenza chimica e agli agenti aggressivi
La resistenza chimica è una proprietà fondamentale per i materiali ceramici destinati ad ambienti industriali, sanitari, laboratori, cucine professionali o aree esterne esposte ad agenti contaminanti. Indica la capacità della superficie ceramica di mantenere inalterate le proprie caratteristiche quando viene a contatto con agenti chimici potenzialmente corrosivi o alteranti.
Meccanismi di attacco chimico sui materiali ceramici
L’aggressione chimica può avvenire per solubilizzazione selettiva dei componenti vetrosi, per alterazione del colore, opacizzazione, formazione di macchie o modifiche superficiali. I materiali più suscettibili sono quelli con una fase vetrosa instabile o con porosità residua accessibile, che facilita la penetrazione di liquidi reattivi.
L’azione può essere:
- superficiale, con perdita di lucentezza o variazioni cromatiche
- strutturale, nei casi più gravi, con indebolimento della superficie smaltata
Resistenza agli acidi, basi e solventi organici
Le superfici ceramiche smaltate correttamente vetrificate presentano in genere una buona resistenza a:
- acidi organici (es. acido citrico, lattico)
- acidi inorganici diluiti (es. acido cloridrico, solforico)
- basi alcaline (es. soda caustica, ammoniaca)
- solventi organici (es. alcol, detergenti professionali)
Tuttavia, le prestazioni dipendono dalla composizione dello smalto, dal livello di cottura e dalla finitura. Una superficie porosa o non completamente sinterizzata può essere più esposta all’attacco chimico.
Comportamento in presenza di sali e agenti atmosferici
L’esposizione a sali disgelanti (come cloruro di sodio o calcio), piogge acide, umidità e agenti atmosferici può nel tempo alterare l’aspetto e la funzionalità delle superfici non adeguatamente protette. In ambienti esterni è quindi fondamentale utilizzare prodotti impermeabili, con vetrificazione completa e assorbimento d’acqua minimo.
Anche le condizioni di posa (giunti, sigillature, pendenza) incidono sulla capacità del materiale di resistere a lungo in condizioni ambientali severe.
Test di resistenza chimica secondo normative internazionali
Le prestazioni dei materiali ceramici contro agenti chimici sono regolate da standard internazionali:
- ISO 10545-13: verifica la resistenza delle piastrelle smaltate all’attacco chimico da acidi e basi, classificate secondo il tipo di alterazione visibile o rilevabile
- ISO 10545-14: valuta la resistenza alle macchie, importante soprattutto per superfici utilizzate in contesti sanitari, domestici o commerciali
I campioni sono sottoposti a esposizione prolungata con sostanze aggressive, e il risultato viene classificato in funzione dell’effetto prodotto (nessun cambiamento, opacizzazione, variazione di colore, ecc.).
Il ruolo dei materiali vetrificanti nella resistenza
Gli smalti ceramici e i materiali vetrificanti svolgono una funzione fondamentale nel determinare le prestazioni superficiali del prodotto finito, incidendo direttamente sulla resistenza meccanica, chimica e all’usura.
Come smalti e materiali vetrificanti influenzano le proprietà di resistenza
Lo smalto rappresenta lo strato esterno del materiale ceramico e può essere formulato per offrire:
- maggiore resistenza all’abrasione (grazie alla presenza di fasi vetrose dure e stabili)
- protezione contro gli agenti chimici e le macchie
- resistenza a shock termici e sbalzi ambientali
Inoltre, un’applicazione uniforme dello smalto e una buona compatibilità di dilatazione termica con il supporto evitano distacchi o microfessurazioni nel tempo.
Formulazioni specifiche per incrementare la resistenza superficiale
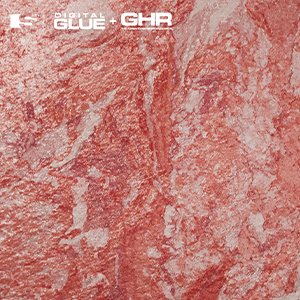
I materiali vetrificanti ad alte prestazioni vengono sviluppati attraverso combinazioni calibrate di fritta, graniglie, pigmenti e additivi, con l’obiettivo di migliorare:
- la compattezza dello strato superficiale
- la resistenza ai graffi e all’usura
- la resistenza alla corrosione chimica
Tecnologie innovative per il miglioramento delle prestazioni
L’evoluzione delle tecnologie ceramiche ha portato allo sviluppo di materiali vetrificanti:
- ready-to-use, per un’applicazione rapida e controllata
- con additivi funzionali integrati per aumentare resistenza e adesione
- adatti a cicli di cottura ottimizzati per la stabilità delle superfici
Queste soluzioni sono progettate per ridurre i difetti estetici e garantire performance elevate anche in ambienti ad alta sollecitazione.
Bilanciamento tra estetica e proprietà tecniche negli smalti
Una delle principali sfide nella progettazione degli smalti ceramici è ottenere un equilibrio efficace tra prestazioni tecniche (resistenza all’usura, facilità di pulizia, compatibilità termica) e qualità estetica (brillantezza, profondità, uniformità). Smalti ad alta durezza devono comunque:
- mantenere la brillantezza o l’opacità desiderata
- garantire un’ottima resa cromatica, anche su grafiche complesse
- assicurare uniformità e stabilità superficiale su grandi formati
Sicer affronta questa sfida con una ricerca continua su materie prime, pigmenti, fritti e additivi, sviluppati per essere perfettamente integrabili nei cicli produttivi più evoluti.
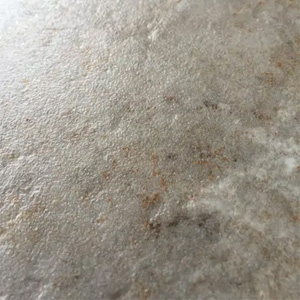
Un esempio concreto è la serie GRA – Dry Lux, progettata per applicazione a secco con successiva lappatura a specchio. Queste graniglie trasparenti e compatte consentono di ottenere superfici ad altissima brillantezza, con totale trasparenza vetrosa, resistenza ai graffi, ottima pulibilità e un coefficiente di dilatazione termica controllato. La loro struttura minimamente porosa e la risposta ottica ottimizzata permettono di esaltare i colori digitali, garantendo risultati estetici di eccellenza su tutti i formati.Sicer si conferma così un partner tecnologico per le aziende ceramiche che cercano materiali di rivestimento ad alte prestazioni, capaci di soddisfare sia requisiti funzionali che aspettative estetiche sempre più sofisticate.
Controllo qualità e ottimizzazione della resistenza
Il mantenimento delle prestazioni dei materiali ceramici dipende in larga parte dal controllo delle fasi di processo. Un sistema efficace di controllo qualità consente di verificare la costanza delle proprietà meccaniche, chimiche e superficiali, e di correggere eventuali deviazioni che comprometterebbero la resistenza finale del prodotto.
Metodologie per il controllo delle proprietà di resistenza in produzione
Le aziende ceramiche adottano protocolli di campionamento e test periodici su lotti di produzione, con prove eseguite in conformità alle normative internazionali (es. ISO 10545). Le proprietà monitorate includono:
- resistenza a flessione (ISO 10545-4)
- resistenza all’abrasione (ISO 10545-7)
- shock termico (ISO 10545-9)
- resistenza chimica e macchie (ISO 10545-13, -14)
I risultati vengono confrontati con le specifiche tecniche attese, e possono essere registrati in sistemi di controllo statistico di processo (SPC) per garantire la tracciabilità e l’efficienza.
Parametri di processo che influenzano la resistenza finale
Le principali variabili che influenzano le prestazioni meccaniche e superficiali del materiale includono:
- temperatura e curva di cottura
- tempo di permanenza al picco
- grado di pressatura e compattazione dell’impasto
- umidità residua nei pezzi crudi
- distribuzione della granulometria
Anche piccole variazioni in questi parametri possono modificare la porosità residua, la sinterizzazione e la coesione interna della struttura ceramica, influendo negativamente sulla resistenza.
Tecniche di ottimizzazione dei cicli di cottura per massimizzare la resistenza
Il ciclo di cottura è uno degli elementi più critici per ottenere superfici ceramiche performanti. Le tecniche di ottimizzazione includono:
- regolazione fine della curva di riscaldamento e raffreddamento
- mantenimento stabile della temperatura di picco
- adattamento del ciclo al tipo di smalto o materiale vetrificante utilizzato
L’obiettivo è ottenere una vetrificazione omogenea, evitando tensioni interne, bolle, difetti di superficie o disomogeneità che potrebbero indebolire il prodotto.
Correlazione tra composizione chimica e proprietà finali
La composizione chimica dell’impasto e dello smalto influenza direttamente la resistenza del materiale. La scelta e il dosaggio di:
- fondenti (borati, alcalini)
- materiali refrattari (silice, allumina)
- additivi specifici (opacizzanti, stabilizzanti)
devono essere studiati in funzione del risultato prestazionale desiderato. L’equilibrio tra fasi cristalline e vetrose, il grado di reattività tra i componenti e la compatibilità termica tra smalto e supporto sono elementi determinanti per ottenere materiali resistenti, duraturi e conformi agli standard qualitativi di mercato.
Innovazioni tecnologiche per migliorare la resistenza
Il settore ceramico sta evolvendo rapidamente grazie all’introduzione di nuove tecnologie e formulazioni orientate all’aumento delle prestazioni. Le innovazioni si concentrano sul potenziamento della resistenza meccanica, chimica e termica, per rispondere alle esigenze dei contesti applicativi più severi.
Additivi e materiali funzionali per l’incremento delle proprietà meccaniche
L’integrazione di additivi funzionali nelle formulazioni di smalti e supporti rappresenta una strategia efficace per migliorare le prestazioni. Tra le soluzioni più utilizzate nel settore:
- utilizzo di graniglie ad alta durezza per rinforzare la superficie smaltata
- ottimizzazione della distribuzione granulometrica per aumentare la densità e ridurre la porosità
- introduzione di opacizzanti stabili per rinforzare la coesione superficiale
Queste soluzioni contribuiscono ad aumentare la tenuta all’usura e la stabilità in ambienti chimicamente aggressivi o soggetti a stress meccanici frequenti.
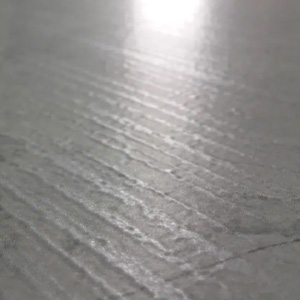
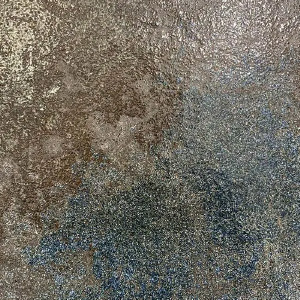
Tecnologie di trattamento superficiale avanzate
Oltre alla composizione, le performance superficiali sono migliorabili anche mediante trattamenti fisico-chimici applicati nella fase finale del processo produttivo. Tra le pratiche comuni:
- utilizzo di smalti autopulenti o antibatterici tramite integrazione di specifici componenti
- tecniche di cottura multistadio che ottimizzano la distribuzione delle tensioni interne
- miglioramento della compatibilità termo-meccanica tra smalto e supporto
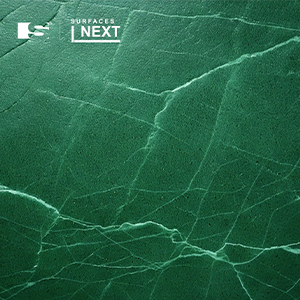
Nel caso dei prodotti NEXT EXPERIENCE SURFACES di Sicer, l’innovazione risiede nella miscela ready-to-use con micrograniglie calibrate, che consente una stesura omogenea, ottima pulibilità e alta resistenza agli agenti chimici e all’abrasione.
Sviluppi nella formulazione di materiali ad alta resistenza
La ricerca ceramica ha permesso di definire formulazioni ad hoc per applicazioni specifiche, agendo sui seguenti aspetti:
- selezione di fritte ad alto contenuto di silice o allumina
- controllo della cristallizzazione delle fasi vetrose per migliorare la compattezza
- studio dei comportamenti a ciclo termico per garantire la stabilità in condizioni reali di utilizzo
Le formulazioni sono testate secondo i principali standard ISO per verificarne la stabilità meccanica, chimica e termica.
Prodotti innovativi per applicazioni specifiche ad alto stress
L’innovazione si esprime anche attraverso lo sviluppo di linee prodotto dedicate ad ambienti ad alto carico prestazionale, come:
- pavimentazioni industriali ad alto traffico
- rivestimenti per esterni esposti a gelo, UV e inquinanti
- superfici tecniche per il settore sanitario o agroalimentare
Queste applicazioni richiedono materiali che garantiscano resistenza prolungata e minima manutenzione, abbinata a caratteristiche estetiche personalizzabili.
Applicazioni industriali e scelta dei materiali
La scelta dei materiali ceramici per l’industria non può prescindere da un’accurata valutazione delle prestazioni richieste in relazione al contesto applicativo. Le diverse forme di resistenza – meccanica, chimica, all’usura, termica – devono essere considerate nella fase di progettazione tecnica e specifica del capitolato.
Criteri di selezione basati sui requisiti di resistenza specifici
Ogni ambiente impone condizioni diverse, ed è quindi necessario individuare:
- il tipo di sollecitazioni attese (traffico, carichi, urti, agenti chimici)
- il livello di frequenza e intensità dell’esposizione
- le normative di riferimento applicabili (es. ISO 10545, EN 16165)
A partire da questi dati si può selezionare il corretto sistema ceramico (formulazione + trattamento + posa) in grado di garantire la resistenza minima certificabile e la durabilità nel tempo.
Applicazioni in base alle diverse tipologie di resistenza richieste
Contesto applicativo | Resistenza prioritaria | Esempio di materiale idoneo |
Ambienti industriali e logistica | Abrasione, compressione | Gres tecnico con finitura strutturata |
Settore alimentare e sanitario | Agenti chimici, macchie | Superfici smaltate vetrificate |
Esterni in clima freddo/umido | Gelo, shock termico | Gres porcellanato basso assorbimento |
Settori ad alta affluenza (commerciale) | Usura, impatto, facilità pulizia | Superfici con classificazione PEI 4-5 |
’associazione tra tipo di ambiente e resistenza richiesta è un passaggio fondamentale per evitare danni prematuri o costi imprevisti di manutenzione e sostituzione.
Correlazione tra costi, prestazioni e livelli di resistenza
La progettazione di superfici ad alte prestazioni comporta un investimento iniziale maggiore, ma assicura un ciclo di vita più lungo e una riduzione dei costi indiretti. Le aziende del settore edilizio e industriale stanno progressivamente adottando soluzioni che massimizzano:
- la durabilità tecnica certificata
- la resistenza all’usura programmata
- la facilità di pulizia e igienizzazione
Questa visione è coerente con un approccio life cycle cost (LCC) e orientato alla sostenibilità economica dell’investimento.
Tendenze future nello sviluppo di materiali ad alta resistenza
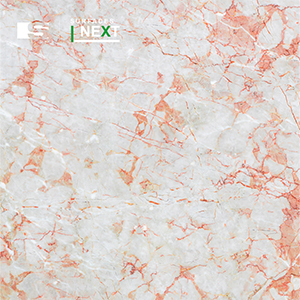
Tra le principali direzioni evolutive nel settore ceramico:
- ampliamento dell’offerta di formulazioni ready-to-use ad alte prestazioni
- introduzione di superfici con funzionalità integrate (es. antiscivolo, autopulenti, antibatteriche)
- ottimizzazione dei processi per ridurre il consumo energetico e aumentare l’efficienza termica
- crescente attenzione alla sostenibilità delle materie prime e ai cicli produttivi a basso impatto ambientale
Sicer, attraverso il costante aggiornamento delle proprie soluzioni e il lavoro del reparto R&D, risponde a queste sfide proponendo materiali evoluti come NEXT EXPERIENCE SURFACES, capaci di unire elevate prestazioni tecniche a risultati estetici contemporanei e applicabilità industriale.
Conclusione
Comprendere come funziona la resistenza ceramica significa saper analizzare ogni aspetto del materiale: dalla sua composizione, alla microstruttura, ai trattamenti superficiali. I test normativi rappresentano uno strumento fondamentale per garantire che i prodotti siano adatti alle condizioni d’uso previste. Soluzioni come NEXT EXPERIENCE SURFACES dimostrano come sia possibile integrare alte prestazioni con facilità d’uso e caratteristiche tecniche avanzate.
FAQ
Dipende dal tipo di materiale e dal test applicato. Viene misurata secondo normative specifiche (es. ISO 10545-4 per la flessione).
Stabilità strutturale, durabilità, resistenza a usura, agenti chimici e variazioni termiche. Le piastrelle ceramiche sono ideali per applicazioni industriali e commerciali.
Questa domanda si riferisce a componenti elettronici, non trattati in questo articolo. Qui si parla della resistenza strutturale delle ceramiche in edilizia e industria.
Le NEXT EXPERIENCE SURFACES sono micrograniglie opache e antiriflesso, ideali per superfici tecniche facilmente pulibili. Le graniglie GHR sono pensate per ambienti ad alto stress: offrono alta resistenza all’abrasione e ottima resa grafica. La serie GRA è specifica per applicazioni a secco e lappatura a specchio, ideale per ottenere superfici estremamente brillanti e compatte.
Sì. Tutte le graniglie della gamma GHR e GRA sono testate per garantire resistenza ad acidi (HCl 3% e 18%) e a condizioni chimiche aggressive, come riportato nei test tecnici inclusi nelle schede prodotto ufficiali.
Sì, le GHR sono adatte ad applicazioni esterne. La loro resistenza all’abrasione, la trasparenza e la possibilità di creare superfici antiscivolo le rendono ideali anche per pavimentazioni esposte a traffico intenso o agenti atmosferici.
Le graniglie GRA permettono la creazione di superfici lappate ad alta brillantezza, con ottima planarità, resistenza ai graffi e assenza di microporosità, migliorando così l’efficienza produttiva e la qualità estetica finale.